Sean did most of the welding while also
teaching. It was critical path stuff.
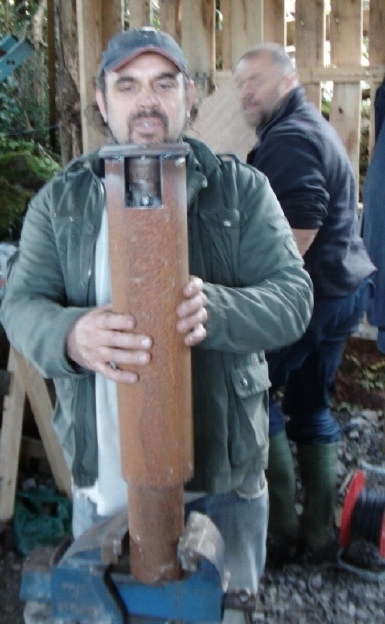
A new idea for the yaw tube head. Gaps for inspection, insertion,
and greasing.
Smaller bore socket for ease of turning.
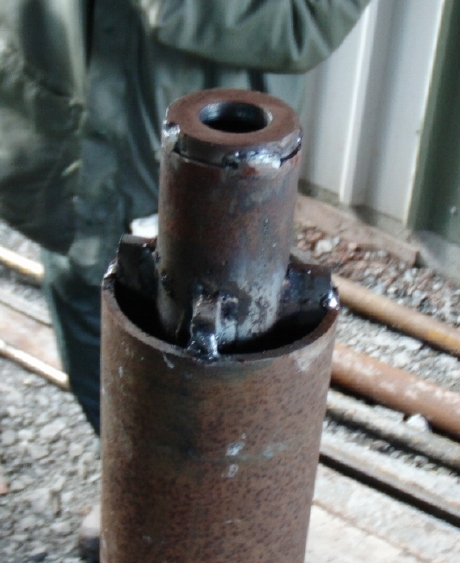
Mast head piece. The top plate is an offcut from the hole saw.
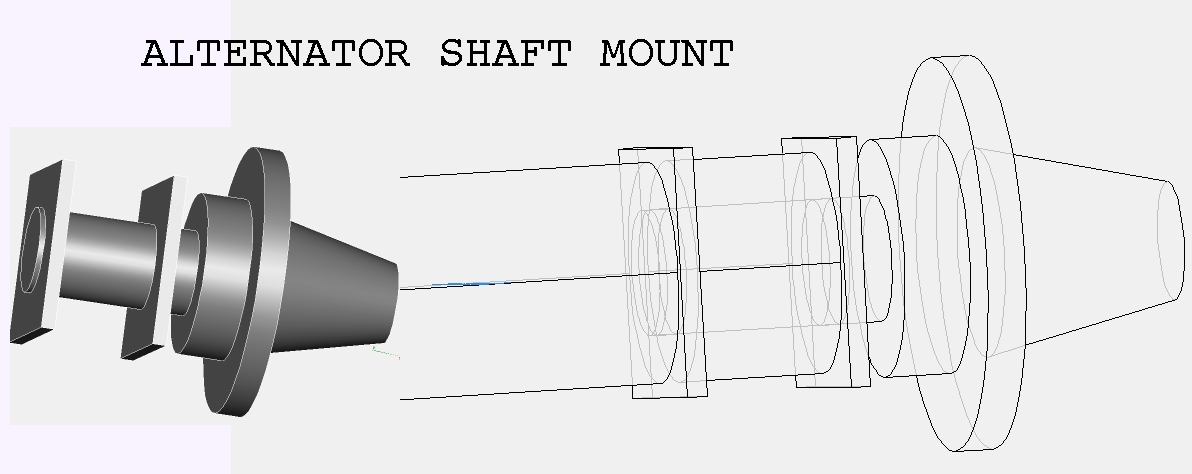
The alternator bearing was off an agricultural machine. It has a
50 mm spindle.
Above is how we welded the spindle into its supporting 3" pipe.
We used a hole saw to cut the square plates, and then the offcuts as
washers in the yaw bearing.
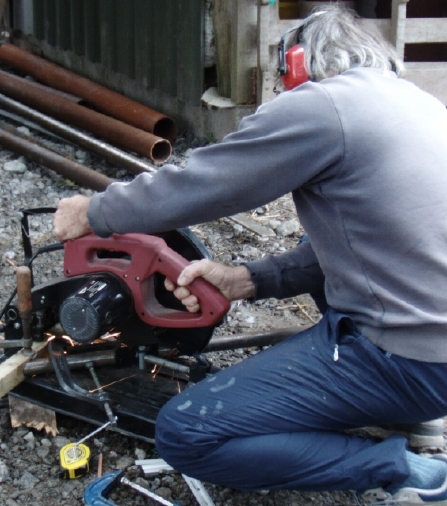
Cutting 45 degree ends on pieces of 1" pipe for the stator mounts.
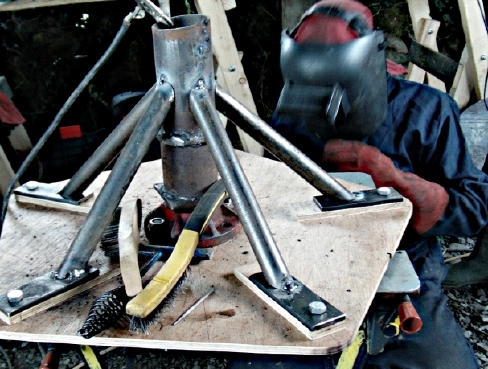
Stator mounts set-up using stator offcut.
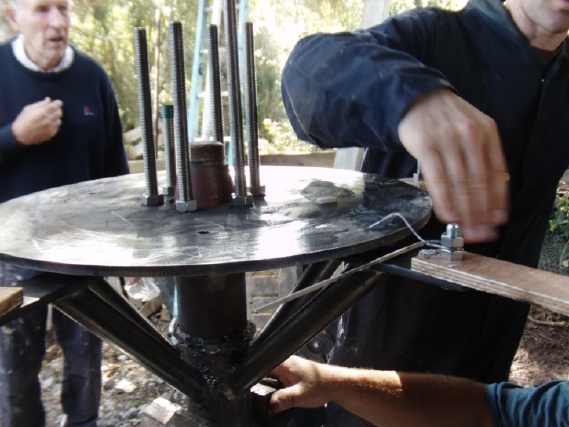
Checking the steel disk and grinding off the highest wobbles.